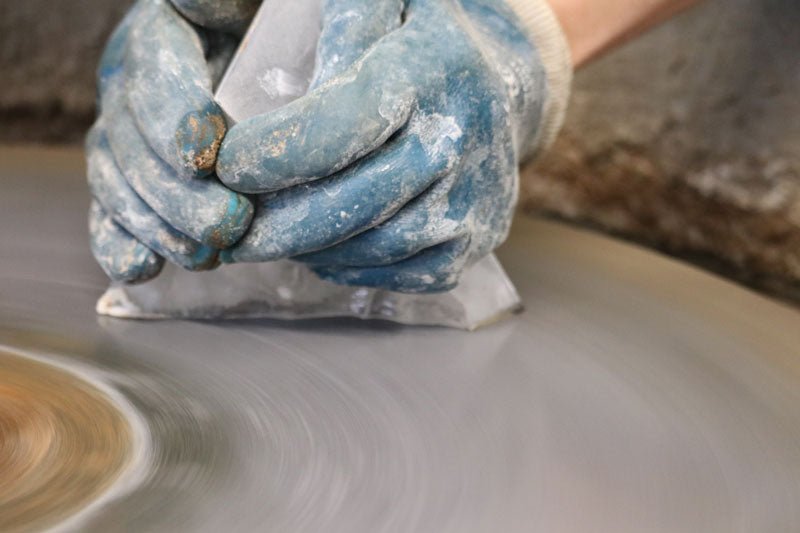
Processes
Casting glass is a fascinating and intricate process that involves melting glass and then shaping it into a desired form or design. Here is an overview of the general steps involved in casting glass:
Gathering Raw Materials: The process begins with gathering the raw materials needed for glassmaking. These materials typically include silica sand, soda ash (sodium carbonate), and limestone (calcium carbonate). Other additives and colorants can be included depending on the desired properties and appearance of the glass.
Melting the Glass: The raw materials are mixed and then heated to high temperatures in a furnace (often referred to as a glass furnace or glass kiln). The heat causes the materials to fuse together and form a molten glass. The temperature required for melting glass varies depending on the specific type of glass being produced.
Mold Preparation: The next step involves preparing the molds for casting. Molds can be made from a variety of materials, including plaster, metal, or refractory materials designed to withstand the high temperatures of the molten glass. The molds are often created in the shape of the desired glass object.
Casting Process:
Blown Glass Casting: In this method, a molten glass gather is blown into the mold, taking on its shape.
Pâte de Verre: This technique involves creating a paste-like mixture of crushed glass and a binder. The paste is carefully placed into the mold, and the mold is fired to melt the glass, leaving behind a solid glass object.
Lost Wax Casting: A wax or other material replica of the desired glass object is created and then encased in a refractory material. The wax is melted or burned out, leaving a cavity in the refractory material. Molten glass is poured into the cavity to take on the shape of the original wax model.
Cooling and Annealing: Once the glass has been cast into the mold, it is allowed to cool slowly to room temperature. This process, known as annealing, helps relieve internal stresses in the glass and ensures that it cools uniformly. Rapid cooling can lead to cracks or other defects in the glass.
Finishing and Polishing: After the glass has cooled and solidified, it is carefully removed from the mold. The glass object may require additional finishing, such as cutting, grinding, polishing, or etching to achieve the desired appearance and surface quality.
Quality Control: Glass castings are often subjected to rigorous quality control measures to check for imperfections or defects.
Decorative Techniques: Depending on the artistic goals, additional decorative techniques such as engraving, painting, or gilding may be applied to the finished glass object.
Final Inspection and Packaging: The completed glass objects are inspected for quality, and once they meet the desired standards, they are carefully packaged for distribution or display.